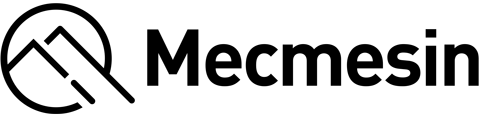
Force testing for watch components and attachments
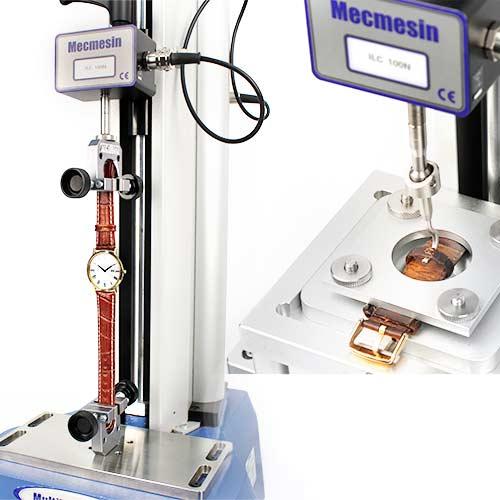
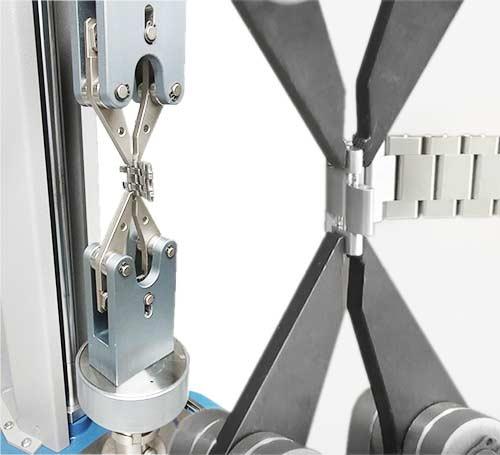
Solution
- Tensile and compression tester with motor drive and software control
- Loadcell appropriate to expected force values
- Fixturing to locate the specimen and apply loading to small components
Benefits
- Accurate results to optimise quality feel and product longevity
- Repeatable testing for multiple design elements
- Confidence in customer quality perception and functional performance
Requirement
The time displayed on our mobile phones and other digital devices will always be more accurate than the time displayed on even the most skilfully engineered mechanical watch—so why does the watch industry continue to thrive? Maybe because “It’s nice to have something mechanical when you’re surrounded so much by the digital world.”
Whatever the motivation for investing in a wristwatch, it needs to stand up to the rigours of everyday use and exude the quality to which the brand associates. That’s why testing the physical strength of the components of your timepiece is such an important part of the watch producers’ quality-control processes.
Solutions
Mecmesin tensile and compression testing equipment is relied upon by major, internationally-recognised, watch producers to give consistency and repeatability for a whole host of tests.
The perfect functioning of crowns, push-pieces and similar control features depends on their smooth operation when pushed and pulled.
Silicone, metal and leather straps all undergo strength tests to make sure they don’t detach too easily from their clasps and buckles and are the subject of the tyest standards NF S86-604 (metallic bracelets) and NF S86-606 (leather and non-metallic bracelets)… even the bonded joint of free loops on straps is tested for its integrity.
Watches classed as diving watches may be subjected to test standard ISO 6425 (Divers’ watches). Some manufacturers models mark this standard on their products’ casebacks. In addition to checks for shock, temperature, magnetic and saltwater spray effects, water-resistance testing through the application of force is also covered:
- Strain is applied to the crown and other setting devices and push-pieces.
- Resistance of attachments—the spring bars must be tested to withstand an outside force of 200 N in each direction. This test is designed to ensure the watch stays attached to the strap under normal conditions, but can also be released in case of emergency underwater.
Suitable test systems and appropriate fixturing is needed to securely grip small components and to accurately apply loads at precise locations. Further quality checks can then be performed in-house in addition to those based on published horology standards.
Test equipment

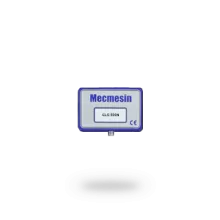
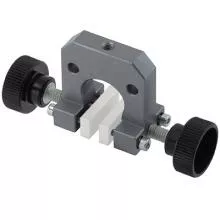